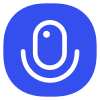
Sign up to save your podcasts
Or
Join me in an interview with Don Yeganeh. Don is a licensed Professional Engineer in New York State and also a Certified Measurement and Verification Professional who graduated from Columbia University as a Mechanical Engineer in 2009. Since then he has spent 6 years as a commissioning engineer and the last 2 years of his professional experience has been with a start-up company Ener.co
In our interview we talk about the existing problems with Air Cooled Condensers and their solution that has a payback in less than a year in some cases. Enercoat® is a performance coating designed to prevent corrosion and increase thermal conductivity, resulting in the most energy efficient condenser coils on the market. Their coating does the following:
and YES they have the field monitoring to prove these results.
Air-cooled heat exchangers lie at the heart of the energy efficiency of air conditioning systems. Weather, environmental conditions, dirt and debris are constantly damaging outdoor cooling equipment. Untreated coils begin to corrode from the first day they are exposed to the elements. There is an estimated 3 – 5% loss in efficiency per year due to corrosion.
“This means that in just 10 years exposure to the elements can impair thermal performance in a coil by 30% to 50%. With the average age of air-cooled units in the U.S. is 21.5 years. This means that 2/3 of cooling capacity has been lost on average by that time.”
Traditional coatings aim to create a smooth fin surface that accumulates less debris over time and protect against fin corrosion. However, traditional fin coatings noticeably impair thermal conductivity – how well heat is transmitted. These coatings possess low levels of conductivity, transfer less heat, and negatively impact energy efficiency. They are also susceptible to tears and cracking, which leaves gaps at the point of the fin-to-tube bond or unfinished edges where fins are cut during the manufacturing process.
Their product Enercoat® addresses all of these issues by:
Why is their coating so special?
They have leveraged graphene nanomaterial technology to create a one-of-a-kind coating that delivers real performance change. Multiwall nanotubes of carbon (CNT) and graphene have a very high thermal conductance. The products twin properties of high thermal conductivity along the axial direction and poor thermal conductivity in the radial direction provide an excellent heat conduction channel that can confine heat currents on the nano scale. Incorporating these at high doses into a polymer produces a stable corrosion protective conductive layer. Application to the metal surfaces of tubes and fins in a heat exchanger ensures the retention of a condenser’s heat exchange capacity. Nano layers of conductive graphene platelets enhance the coating and makes it extremely conductive both electrically and thermally.
Join me in our interview to learn more of the details.
5
22 ratings
Join me in an interview with Don Yeganeh. Don is a licensed Professional Engineer in New York State and also a Certified Measurement and Verification Professional who graduated from Columbia University as a Mechanical Engineer in 2009. Since then he has spent 6 years as a commissioning engineer and the last 2 years of his professional experience has been with a start-up company Ener.co
In our interview we talk about the existing problems with Air Cooled Condensers and their solution that has a payback in less than a year in some cases. Enercoat® is a performance coating designed to prevent corrosion and increase thermal conductivity, resulting in the most energy efficient condenser coils on the market. Their coating does the following:
and YES they have the field monitoring to prove these results.
Air-cooled heat exchangers lie at the heart of the energy efficiency of air conditioning systems. Weather, environmental conditions, dirt and debris are constantly damaging outdoor cooling equipment. Untreated coils begin to corrode from the first day they are exposed to the elements. There is an estimated 3 – 5% loss in efficiency per year due to corrosion.
“This means that in just 10 years exposure to the elements can impair thermal performance in a coil by 30% to 50%. With the average age of air-cooled units in the U.S. is 21.5 years. This means that 2/3 of cooling capacity has been lost on average by that time.”
Traditional coatings aim to create a smooth fin surface that accumulates less debris over time and protect against fin corrosion. However, traditional fin coatings noticeably impair thermal conductivity – how well heat is transmitted. These coatings possess low levels of conductivity, transfer less heat, and negatively impact energy efficiency. They are also susceptible to tears and cracking, which leaves gaps at the point of the fin-to-tube bond or unfinished edges where fins are cut during the manufacturing process.
Their product Enercoat® addresses all of these issues by:
Why is their coating so special?
They have leveraged graphene nanomaterial technology to create a one-of-a-kind coating that delivers real performance change. Multiwall nanotubes of carbon (CNT) and graphene have a very high thermal conductance. The products twin properties of high thermal conductivity along the axial direction and poor thermal conductivity in the radial direction provide an excellent heat conduction channel that can confine heat currents on the nano scale. Incorporating these at high doses into a polymer produces a stable corrosion protective conductive layer. Application to the metal surfaces of tubes and fins in a heat exchanger ensures the retention of a condenser’s heat exchange capacity. Nano layers of conductive graphene platelets enhance the coating and makes it extremely conductive both electrically and thermally.
Join me in our interview to learn more of the details.