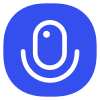
Sign up to save your podcasts
Or
Manjish Naik and Sarah Lukens join us to discuss how to overcome data quality issues with KPIs.
They’ll help us understand:
What is a KPI?
A Key Performance Indicator (KPI) measures the performance of an asset in either a process or manufacturing plant. The metrics can be high-level, for instance Overall Equipment Effectiveness (OEE), or granular like corrective or reactive count.
KPI metrics can fall into two categories – leading or lagging. Leading metrics give you a forecast of what’s to come. An example is PM compliance. By meeting your PM schedule, it would allow you to find issues in advance, making you more proactive towards fixing arising issues. Lagging indicators like reactive count, take into account something that’s already happened, to analyze and improve future processes.
Having a varied system of KPIs to work with helps you to better understand your asset performance in the field.
How to get started with data
KPIs have been known to bring about issues such as inconsistent measurements and inconsistent data. So, how do we get past these? It all starts with the quality of the data. These are a few questions you need to answer:
Data quality refers to its fitness to a given purpose. It needs to be complete enough to allow you to measure and understand critical indicators.
How to establish KPIs
KPIs get calculated from the maintenance work done physically. It can also be calculated from your Computerized Maintenance Management System (CMMS), like SAP or Maximo. The process starts with you understanding how many failures happened within a specific period. You could establish this by talking to floor technicians (which isn’t very scalable), or relying on data from CMMS
The data quality from a CMMS is preferred as it helps understand how metrics get calculated, and what insights come out. A CMMS has predefined fields for cost, parts, labor, skill type, activity type, among others. However, these still don’t guarantee quality of the collected data.
Factors hindering the accuracy of data quality
There are three main factors:
There are organizations trying to streamline data quality issues. These include:
However, even with these organizations, we still can’t measure data correctly. That’s because:
How to overcome data quality issues
Rather than storing the CMMS data you need to be able to extract this information in a scalable way. Natural Language Processing (NLP) approaches, responsible for programming computers and algorithms, can be used to extract and refine historical data.
Is it worth it to go back and clean the data, or should the organization move forward collecting new data?
The answer depends on whether you can afford the cost, and if you’ll get value at the end of the process.Fundamentally, it’s worth it if you can go at least five years or a decade in the past, and no more. So, rather than paying to create and store data, organizations should unlock historical data. It’s necessary to focus on unlocking valuable assets rather than every stored asset to get the most value.
Take a holistic approach on aspects like:
How can you improve your current data quality?
Start by measuring your data quality to separate the good data from the bad. For the not so good data, find out what makes it substandard. You can also start implementing best practices at your organization. As for your historical data, start using NLP processes to extract and make use of what you already have.
How to become successful with data quality
You need the correct mindset to start getting good quality data. Also, don’t get overwhelmed and don’t procrastinate. This will help you to sustain your improvements through regular monitoring and tracking of the system.
Eruditio Links:
Manjish Naik & Sarah Lukens Links:
Rooted In Reliability podcast is a proud member of Reliability.fm network. We encourage you to please rate and review this podcast on iTunes and Stitcher. It ensures the podcast stays relevant and is easy to find by like-minded professionals. It is only with your ratings and reviews that the Rooted In Reliability podcast can continue to grow. Thank you for providing the small but critical support for the Rooted In Reliability podcast!
The post 204-Data Quality Issues with Manjish Naik & Sarah Lukens appeared first on Accendo Reliability.
4.8
2828 ratings
Manjish Naik and Sarah Lukens join us to discuss how to overcome data quality issues with KPIs.
They’ll help us understand:
What is a KPI?
A Key Performance Indicator (KPI) measures the performance of an asset in either a process or manufacturing plant. The metrics can be high-level, for instance Overall Equipment Effectiveness (OEE), or granular like corrective or reactive count.
KPI metrics can fall into two categories – leading or lagging. Leading metrics give you a forecast of what’s to come. An example is PM compliance. By meeting your PM schedule, it would allow you to find issues in advance, making you more proactive towards fixing arising issues. Lagging indicators like reactive count, take into account something that’s already happened, to analyze and improve future processes.
Having a varied system of KPIs to work with helps you to better understand your asset performance in the field.
How to get started with data
KPIs have been known to bring about issues such as inconsistent measurements and inconsistent data. So, how do we get past these? It all starts with the quality of the data. These are a few questions you need to answer:
Data quality refers to its fitness to a given purpose. It needs to be complete enough to allow you to measure and understand critical indicators.
How to establish KPIs
KPIs get calculated from the maintenance work done physically. It can also be calculated from your Computerized Maintenance Management System (CMMS), like SAP or Maximo. The process starts with you understanding how many failures happened within a specific period. You could establish this by talking to floor technicians (which isn’t very scalable), or relying on data from CMMS
The data quality from a CMMS is preferred as it helps understand how metrics get calculated, and what insights come out. A CMMS has predefined fields for cost, parts, labor, skill type, activity type, among others. However, these still don’t guarantee quality of the collected data.
Factors hindering the accuracy of data quality
There are three main factors:
There are organizations trying to streamline data quality issues. These include:
However, even with these organizations, we still can’t measure data correctly. That’s because:
How to overcome data quality issues
Rather than storing the CMMS data you need to be able to extract this information in a scalable way. Natural Language Processing (NLP) approaches, responsible for programming computers and algorithms, can be used to extract and refine historical data.
Is it worth it to go back and clean the data, or should the organization move forward collecting new data?
The answer depends on whether you can afford the cost, and if you’ll get value at the end of the process.Fundamentally, it’s worth it if you can go at least five years or a decade in the past, and no more. So, rather than paying to create and store data, organizations should unlock historical data. It’s necessary to focus on unlocking valuable assets rather than every stored asset to get the most value.
Take a holistic approach on aspects like:
How can you improve your current data quality?
Start by measuring your data quality to separate the good data from the bad. For the not so good data, find out what makes it substandard. You can also start implementing best practices at your organization. As for your historical data, start using NLP processes to extract and make use of what you already have.
How to become successful with data quality
You need the correct mindset to start getting good quality data. Also, don’t get overwhelmed and don’t procrastinate. This will help you to sustain your improvements through regular monitoring and tracking of the system.
Eruditio Links:
Manjish Naik & Sarah Lukens Links:
Rooted In Reliability podcast is a proud member of Reliability.fm network. We encourage you to please rate and review this podcast on iTunes and Stitcher. It ensures the podcast stays relevant and is easy to find by like-minded professionals. It is only with your ratings and reviews that the Rooted In Reliability podcast can continue to grow. Thank you for providing the small but critical support for the Rooted In Reliability podcast!
The post 204-Data Quality Issues with Manjish Naik & Sarah Lukens appeared first on Accendo Reliability.