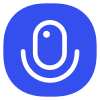
Sign up to save your podcasts
Or
We're excited to have Wesley Cash to shed light on proper greasing techniques. He’s been at Noria Corporation for nine years now and is currently their director of technical services. However, his professional experience in fields relating to reliability, lubrication, and maintenance spans over 16 years, enabling him to acquire numerous ICML and CLS certifications.
He’ll help us learn more on what’s necessary for proper greasing practices, such as:
Why is lubrication necessary?
Lubrication is a fundamental process of your reliability program. That’s because it’s one of the leading causes of equipment failures. Without proper lubrication, you increase your chance of failures. It’ll also cause misses with other predictive technology you’re using.
Research shows that 90% of all bearing failures relate to lubrication issues. Lubricant issues also account for up to 80% of hydraulic failures. In general, lubrication issues account for nearly half of all equipment failures. These could include having too much or too little lubrication. It could also be having contaminated lubricants.
How many people use grease guns properly?
Less than 25% of people using grease guns do so correctly. These problems result from factors like not getting adequate training. That’s because using a grease gun isn’t seen as a difficult task. The complexity comes in knowing how much grease you need to add. Most maintenance people learn how to operate a grease gun through work experiences. You’ll often find those in that role assuming the process is self-explanatory.
Common issues from using a grease gun
You can divide these into two groups. These are:
How to properly use a grease gun
For starters, try to add a lubricant while the equipment is running. It’s understandable if you can’t do this due to safety concerns. But, if possible, first look for a purge fitting or plug. It’ll serve as a relief port or pathway for old grease to get pushed out. By doing this, you’ll also reduce the pressure that comes with greasing equipment.
Before attaching the grease gun, clean the grease fitting. Wipe with a lint-free towel. Remove any plastic fittings you find on it. Then purge some grease from the grease gun before attaching to the grease fitting. That helps to clean the end of the grease gun, especially if it was in storage.
You can then slowly start to apply the grease. When you disconnect the grease gun, leave a small amount of grease. It should be enough to cover the fitting, sealing it from contaminants. If you have a plastic cap, use that to cover it. Run your machine for between 10-20 minutes if it has a relief port. That will allow any excess pressure to come out.
Importance of keeping out contaminants
With cleaning up greased fittings, maintenance-induced failures due to contamination are frequent. With oil lubricated parts, you can filter out solid contaminants. With greased parts, the contaminants stay firmly in place. Since it isn’t an aqueous solution, contaminants can’t easily get pushed out.
Other factors to enhance proper lubrication
These include elements such as:
Tips to improve your lubrication program
In summary
You should avoid fixing bad habits within your plant by spending money. Use incremental changes to create changes. Check the lubricant life cycle by asking the following questions:
In general, most issues arise from the storage and handling of lubricants. So start small and make sustainable changes. Develop a roadmap of what needs to get done.
Eruditio Links:
Wesley Cash Links:
Rooted In Reliability podcast is a proud member of Reliability.fm network. We encourage you to please rate and review this podcast on iTunes and Stitcher. It ensures the podcast stays relevant and is easy to find by like-minded professionals. It is only with your ratings and reviews that the Rooted In Reliability podcast can continue to grow. Thank you for providing the small but critical support for the Rooted In Reliability podcast!
The post 216-Proper Greasing with Wesley Cash appeared first on Accendo Reliability.
4.8
2828 ratings
We're excited to have Wesley Cash to shed light on proper greasing techniques. He’s been at Noria Corporation for nine years now and is currently their director of technical services. However, his professional experience in fields relating to reliability, lubrication, and maintenance spans over 16 years, enabling him to acquire numerous ICML and CLS certifications.
He’ll help us learn more on what’s necessary for proper greasing practices, such as:
Why is lubrication necessary?
Lubrication is a fundamental process of your reliability program. That’s because it’s one of the leading causes of equipment failures. Without proper lubrication, you increase your chance of failures. It’ll also cause misses with other predictive technology you’re using.
Research shows that 90% of all bearing failures relate to lubrication issues. Lubricant issues also account for up to 80% of hydraulic failures. In general, lubrication issues account for nearly half of all equipment failures. These could include having too much or too little lubrication. It could also be having contaminated lubricants.
How many people use grease guns properly?
Less than 25% of people using grease guns do so correctly. These problems result from factors like not getting adequate training. That’s because using a grease gun isn’t seen as a difficult task. The complexity comes in knowing how much grease you need to add. Most maintenance people learn how to operate a grease gun through work experiences. You’ll often find those in that role assuming the process is self-explanatory.
Common issues from using a grease gun
You can divide these into two groups. These are:
How to properly use a grease gun
For starters, try to add a lubricant while the equipment is running. It’s understandable if you can’t do this due to safety concerns. But, if possible, first look for a purge fitting or plug. It’ll serve as a relief port or pathway for old grease to get pushed out. By doing this, you’ll also reduce the pressure that comes with greasing equipment.
Before attaching the grease gun, clean the grease fitting. Wipe with a lint-free towel. Remove any plastic fittings you find on it. Then purge some grease from the grease gun before attaching to the grease fitting. That helps to clean the end of the grease gun, especially if it was in storage.
You can then slowly start to apply the grease. When you disconnect the grease gun, leave a small amount of grease. It should be enough to cover the fitting, sealing it from contaminants. If you have a plastic cap, use that to cover it. Run your machine for between 10-20 minutes if it has a relief port. That will allow any excess pressure to come out.
Importance of keeping out contaminants
With cleaning up greased fittings, maintenance-induced failures due to contamination are frequent. With oil lubricated parts, you can filter out solid contaminants. With greased parts, the contaminants stay firmly in place. Since it isn’t an aqueous solution, contaminants can’t easily get pushed out.
Other factors to enhance proper lubrication
These include elements such as:
Tips to improve your lubrication program
In summary
You should avoid fixing bad habits within your plant by spending money. Use incremental changes to create changes. Check the lubricant life cycle by asking the following questions:
In general, most issues arise from the storage and handling of lubricants. So start small and make sustainable changes. Develop a roadmap of what needs to get done.
Eruditio Links:
Wesley Cash Links:
Rooted In Reliability podcast is a proud member of Reliability.fm network. We encourage you to please rate and review this podcast on iTunes and Stitcher. It ensures the podcast stays relevant and is easy to find by like-minded professionals. It is only with your ratings and reviews that the Rooted In Reliability podcast can continue to grow. Thank you for providing the small but critical support for the Rooted In Reliability podcast!
The post 216-Proper Greasing with Wesley Cash appeared first on Accendo Reliability.