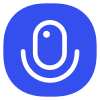
Sign up to save your podcasts
Or
Today, we’re welcoming Rob Kalwarowsky from Rob’s Reliability project. He’s currently an asset manager at Enbridge, handling their mechanical assets. Rob was previously a reliability consultant for five years, as well as a reliability engineer at Teck Resources. He’s been on a few of our previous podcasts.
But today, he’s helping us look into aspects of spare parts optimization such as:
… and so much more!
What is spare parts optimization?
With spare parts optimization, you’re trying to make sure you have the right amount. That’s to help cut the total cost of ownership of your business. So if you’re talking about asset management, you’re maximizing value. Buying too many spare parts, you’re spending too much on holding and purchasing that inventory. If you buy too few, then the cost of the breakdown and waiting for repairs is high. By optimizing, you’ll have the total minimum cost.
What data is necessary to carry out an optimization?
Once you’re looking to optimize, you would need information such as:
Should you choose an advanced or simple approach when optimizing?
If you’ve just started, an advanced approach wouldn’t be ideal for your company. But it also depends on how far you’d like to go. You can add value by using formulas like Economic Order Quantity (EOQ). You could also do an ABC analysis on the likes of Excel spreadsheets.
For a high cost, high lead time component with the data to back it, and the time to do it, a Monte Carlo simulator would work best. It’s not ideal for bolts and other small parts. But with big items like transformers and electric wheel motors, an advanced analytical approach is necessary.
For companies dealing with high-value equipment, advanced strategies show higher success rates. It enables efficient collaboration between different departments. That helps in reducing downtimes on this equipment, which also tend to cost a lot.
For companies with low-cost equipment, min and max formulas or economic order formulas would do
Formulas to help with optimization
The EOQ formula is the most common method used. It’s the annual demand, fixed order cost, and annual storage cost. Using this information from your collected data, you can calculate it out. You can also do inventory turns or look at service order levels for parts you use frequently.
There’s also the ABC analysis. The A parts account for 80% of all parts but only 20%, or less, of the inventory’s value. The B parts are 25% usage but are 30% of inventory stock. The C parts are 5% usage but account for half the inventory’s share.
Spare parts optimization aims to add value. Using methods that take more time for low-value parts brings down your ROI. So focus on equipment that could cost the company more money.
How often should you review your optimization?
The frequency depends on the amount of work your organization allows you to do. Once a year should be enough for most organizations. But if the operating context changes significantly, you may need to check on the high-cost items. If things remain unchanged, though, you can continue to use the same system, reviewing it every couple of years or so. It’s no different than a criticality analysis. A great way to keep track is to have a list. It should include all equipment you need to review if the operating context changes.
What brings about success with spare parts optimization?
Standardize these processes and make them part of your business. Ensure your operations do not rely on a single individual’s presence in the company.
What would make the process easier?
The data plays a crucial role in spare parts optimization. With the issued work orders, you need to look out for the failure data, condition data, and the age of the equipment. That includes items installed decades ago with no information on them available. So making the data easy to get would be ideal. With the data on hand, other processes become more manageable.
In summary
Optimization is more significant than just the spare parts you’re checking. It’s about looking for ways to add value to your company. It’s looking at critical components that when they fail, big things happen. That could be a safety issue, environmental issue, or a production issue. Look at those and figure out how to add value to those specific components. Pick items that are high cost, high value, and follow up on them.
Eruditio Links:
Rob Kalwarowsky Links:
Rooted In Reliability podcast is a proud member of Reliability.fm network. We encourage you to please rate and review this podcast on iTunes and Stitcher. It ensures the podcast stays relevant and is easy to find by like-minded professionals. It is only with your ratings and reviews that the Rooted In Reliability podcast can continue to grow. Thank you for providing the small but critical support for the Rooted In Reliability podcast!
The post 222-Spare Parts Optimization with Rob Kalwarowsky appeared first on Accendo Reliability.
4.8
2828 ratings
Today, we’re welcoming Rob Kalwarowsky from Rob’s Reliability project. He’s currently an asset manager at Enbridge, handling their mechanical assets. Rob was previously a reliability consultant for five years, as well as a reliability engineer at Teck Resources. He’s been on a few of our previous podcasts.
But today, he’s helping us look into aspects of spare parts optimization such as:
… and so much more!
What is spare parts optimization?
With spare parts optimization, you’re trying to make sure you have the right amount. That’s to help cut the total cost of ownership of your business. So if you’re talking about asset management, you’re maximizing value. Buying too many spare parts, you’re spending too much on holding and purchasing that inventory. If you buy too few, then the cost of the breakdown and waiting for repairs is high. By optimizing, you’ll have the total minimum cost.
What data is necessary to carry out an optimization?
Once you’re looking to optimize, you would need information such as:
Should you choose an advanced or simple approach when optimizing?
If you’ve just started, an advanced approach wouldn’t be ideal for your company. But it also depends on how far you’d like to go. You can add value by using formulas like Economic Order Quantity (EOQ). You could also do an ABC analysis on the likes of Excel spreadsheets.
For a high cost, high lead time component with the data to back it, and the time to do it, a Monte Carlo simulator would work best. It’s not ideal for bolts and other small parts. But with big items like transformers and electric wheel motors, an advanced analytical approach is necessary.
For companies dealing with high-value equipment, advanced strategies show higher success rates. It enables efficient collaboration between different departments. That helps in reducing downtimes on this equipment, which also tend to cost a lot.
For companies with low-cost equipment, min and max formulas or economic order formulas would do
Formulas to help with optimization
The EOQ formula is the most common method used. It’s the annual demand, fixed order cost, and annual storage cost. Using this information from your collected data, you can calculate it out. You can also do inventory turns or look at service order levels for parts you use frequently.
There’s also the ABC analysis. The A parts account for 80% of all parts but only 20%, or less, of the inventory’s value. The B parts are 25% usage but are 30% of inventory stock. The C parts are 5% usage but account for half the inventory’s share.
Spare parts optimization aims to add value. Using methods that take more time for low-value parts brings down your ROI. So focus on equipment that could cost the company more money.
How often should you review your optimization?
The frequency depends on the amount of work your organization allows you to do. Once a year should be enough for most organizations. But if the operating context changes significantly, you may need to check on the high-cost items. If things remain unchanged, though, you can continue to use the same system, reviewing it every couple of years or so. It’s no different than a criticality analysis. A great way to keep track is to have a list. It should include all equipment you need to review if the operating context changes.
What brings about success with spare parts optimization?
Standardize these processes and make them part of your business. Ensure your operations do not rely on a single individual’s presence in the company.
What would make the process easier?
The data plays a crucial role in spare parts optimization. With the issued work orders, you need to look out for the failure data, condition data, and the age of the equipment. That includes items installed decades ago with no information on them available. So making the data easy to get would be ideal. With the data on hand, other processes become more manageable.
In summary
Optimization is more significant than just the spare parts you’re checking. It’s about looking for ways to add value to your company. It’s looking at critical components that when they fail, big things happen. That could be a safety issue, environmental issue, or a production issue. Look at those and figure out how to add value to those specific components. Pick items that are high cost, high value, and follow up on them.
Eruditio Links:
Rob Kalwarowsky Links:
Rooted In Reliability podcast is a proud member of Reliability.fm network. We encourage you to please rate and review this podcast on iTunes and Stitcher. It ensures the podcast stays relevant and is easy to find by like-minded professionals. It is only with your ratings and reviews that the Rooted In Reliability podcast can continue to grow. Thank you for providing the small but critical support for the Rooted In Reliability podcast!
The post 222-Spare Parts Optimization with Rob Kalwarowsky appeared first on Accendo Reliability.