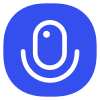
Sign up to save your podcasts
Or
Without printed circuit boards (PCBs), the electronic devices that control, monitor, and regulate everyday life in various environments would not exist. But, this miniaturization of electrical circuits has its challenges when it comes to the manufacturing and assembly of PCBs. Manufacturers must follow industry best practices to ensure these critical components do not fail, even as they speed up the PCB assembly process to meet ever-higher consumer demands.
There exists a close working relationship between PCB designers and manufacturers. Read on for tips on creating a great relationship and accelerating processes.
PCB ASSEMBLY TIP 1: PLAN PCB PROJECTS EARLY
Optimizing PCB assembly requires careful planning, including a clear description of requirements such as the following:
- Bill of materials (BOM)
- Gerber files
- Pick and place the file
- PCBA testing file
Additional information is often needed for the final PCB manufacture, including assembly drawings, 3D drawings, and schematics.
Manufacturers can prepare the fabrication and assembly phases more quickly with detailed documentation and PCB specifications and purchase the needed materials. Consider partnering with other key service providers, like PCB design software creator Altium Designer.
Maintaining clear lines of communication with manufacturers helps ensure that PCBs are only made to standards. Choosing a manufacturer that matches communication style and frequency helps ensure a smoother process.
PCB ASSEMBLY TIP 2: DESIGN FOR MANUFACTURABILITY (DFM)
DFM is a general engineering practice for designing products to make them easy to manufacture. This process allows for easier detection of potential problems in the design phase, which is less expensive than discovering problems during manufacture. Edge clearance, acid traps, layout complexity, and solder masks between pads determine a PCB’s manufacturability.
While DFM is a common practice in virtually all engineering disciplines, the ways it is implemented can vary. For example, each PCB manufacturer uses its guidelines and procedures that can address possible production problems during the design phase.
These include consideration of the manufacturers’ capacity and capabilities, along with industry-wide best practices that are continually evolving.
DFM guidelines should address these measures to avoid delays. Common factors to consider are circuit routing, panalization, and component placement. Minimize the use of complex or obsolete components that can slow down manufacturing and sourcing processes. Preliminary testing is a meaningful way to identify errors early in the design process and avoid the higher cost of fixing them during assembly, which requires rework.
DFM testing can detect problems with footprint corroboration, component spacing, and component polarity, provided it’s performed by experienced engineers specializing in these procedures. Specific benefits of DFM testing include reduced costs, improved product quality, and shorter delivery times.
Read: Design for Manufacturability (DFM) Process Overview
PCB ASSEMBLY TIP 3: GAIN MORE VISIBILITY INTO THE MANUFACTURING PROCESS
The quality of components used in the assembly of PCBs is crucial to the quality of the final product. A professional PCB assembler should have a quality assurance (QA) department that evaluates BOM components based on quality, date, and model number. In addition, assemblers should perform various tests on samples, such as material operational testing. A final inspection of PCB components should be performed to detect any missing or broken parts, circuit deformation, and oxidation.
Choosing the right PCB manufacturer can be particularly challenging in today’s global economy, largely due to the many choices available. However, the United States (US) has some of the highest quality standards in the world, which are enforced by regulatory bodies like the International Organization for Standardization (ISO).
As a result, US-based PCB manufacturers must adhere to high standards that meet or exceed their customers’ expectations. Consider a manufacturer’s certifications when researching the best partner for the project.
PCB ASSEMBLY TIP 4: ALIGN EXPECTATIONS WITH THE PCB MANUFACTURER
Collaboration between PCB designers and manufacturers can eliminate many challenges caused when the manufacturer needs to adequately understand the project’s requirements, specifications, or standards.
Get the design guide: A Guide to Design-for-Manufacturing (DFM) Principles.
The manufacturer should remain closely involved in the design review process, allowing them to provide insights and suggest improvement. In addition, feedback should be offered to the manufacturer after each production run, fostering a culture of continual improvement.
Ensure all team members are in the loop when making design changes. This includes material suppliers that are directly connected to the manufacturer. Some collaboration tools for PCB designers include links to suppliers, and providing real-time data on pricing and quantities.
PCB ASSEMBLY TIP 5: CLEAR AND DETAILED DOCUMENTATION
Documenting a PCB design requires designers to clearly define their work regions, meaning they need to mark out their space on the board. Work regions should remain uncluttered and easy to navigate, so designers can focus on their design rather than struggling with software to provide documentation. These tools should also allow designers to easily view the work of other designers on that board, so they can avoid conflicts or duplicated effort.
PCB ASSEMBLY TIP 6: CONTINUOUS IMPROVEMENT AND FEEDBACK
The PCB assembly process can be improved by following the plan-do-check-act (PDCA) cycle. The Plan phase of this approach identifies opportunities for change and plans those changes. The Do phase implements changes on a small scale, while the Check phase analyzes the results to determine the effects of those changes. If the changes are beneficial, the Act phase implements them wider and continuously assesses the results.
Work with the PCB manufacturer to discover new opportunities for improvement, which is an essential component of DFM. This practice also requires collecting and analyzing data to identify areas to reduce scrap, promote assembly cycle times, and improve quality issues while reducing production bottlenecks.
STRENGTHEN PCB ASSEMBLY PROCESS WITH IMAGINEERING: ESSENTIAL STRATEGIES FOR SUCCESS
Many technological advances have improved the reliability and accuracy of PCB assembly, but the challenge is to make the process as seamless and efficient as possible. The best practices discussed above will help improve assembly, especially when combined with an experienced PCB manufacturer like Imagineering. These changes will ultimately accelerate PCB assembly and reduce time-to-market.
Without printed circuit boards (PCBs), the electronic devices that control, monitor, and regulate everyday life in various environments would not exist. But, this miniaturization of electrical circuits has its challenges when it comes to the manufacturing and assembly of PCBs. Manufacturers must follow industry best practices to ensure these critical components do not fail, even as they speed up the PCB assembly process to meet ever-higher consumer demands.
There exists a close working relationship between PCB designers and manufacturers. Read on for tips on creating a great relationship and accelerating processes.
PCB ASSEMBLY TIP 1: PLAN PCB PROJECTS EARLY
Optimizing PCB assembly requires careful planning, including a clear description of requirements such as the following:
- Bill of materials (BOM)
- Gerber files
- Pick and place the file
- PCBA testing file
Additional information is often needed for the final PCB manufacture, including assembly drawings, 3D drawings, and schematics.
Manufacturers can prepare the fabrication and assembly phases more quickly with detailed documentation and PCB specifications and purchase the needed materials. Consider partnering with other key service providers, like PCB design software creator Altium Designer.
Maintaining clear lines of communication with manufacturers helps ensure that PCBs are only made to standards. Choosing a manufacturer that matches communication style and frequency helps ensure a smoother process.
PCB ASSEMBLY TIP 2: DESIGN FOR MANUFACTURABILITY (DFM)
DFM is a general engineering practice for designing products to make them easy to manufacture. This process allows for easier detection of potential problems in the design phase, which is less expensive than discovering problems during manufacture. Edge clearance, acid traps, layout complexity, and solder masks between pads determine a PCB’s manufacturability.
While DFM is a common practice in virtually all engineering disciplines, the ways it is implemented can vary. For example, each PCB manufacturer uses its guidelines and procedures that can address possible production problems during the design phase.
These include consideration of the manufacturers’ capacity and capabilities, along with industry-wide best practices that are continually evolving.
DFM guidelines should address these measures to avoid delays. Common factors to consider are circuit routing, panalization, and component placement. Minimize the use of complex or obsolete components that can slow down manufacturing and sourcing processes. Preliminary testing is a meaningful way to identify errors early in the design process and avoid the higher cost of fixing them during assembly, which requires rework.
DFM testing can detect problems with footprint corroboration, component spacing, and component polarity, provided it’s performed by experienced engineers specializing in these procedures. Specific benefits of DFM testing include reduced costs, improved product quality, and shorter delivery times.
Read: Design for Manufacturability (DFM) Process Overview
PCB ASSEMBLY TIP 3: GAIN MORE VISIBILITY INTO THE MANUFACTURING PROCESS
The quality of components used in the assembly of PCBs is crucial to the quality of the final product. A professional PCB assembler should have a quality assurance (QA) department that evaluates BOM components based on quality, date, and model number. In addition, assemblers should perform various tests on samples, such as material operational testing. A final inspection of PCB components should be performed to detect any missing or broken parts, circuit deformation, and oxidation.
Choosing the right PCB manufacturer can be particularly challenging in today’s global economy, largely due to the many choices available. However, the United States (US) has some of the highest quality standards in the world, which are enforced by regulatory bodies like the International Organization for Standardization (ISO).
As a result, US-based PCB manufacturers must adhere to high standards that meet or exceed their customers’ expectations. Consider a manufacturer’s certifications when researching the best partner for the project.
PCB ASSEMBLY TIP 4: ALIGN EXPECTATIONS WITH THE PCB MANUFACTURER
Collaboration between PCB designers and manufacturers can eliminate many challenges caused when the manufacturer needs to adequately understand the project’s requirements, specifications, or standards.
Get the design guide: A Guide to Design-for-Manufacturing (DFM) Principles.
The manufacturer should remain closely involved in the design review process, allowing them to provide insights and suggest improvement. In addition, feedback should be offered to the manufacturer after each production run, fostering a culture of continual improvement.
Ensure all team members are in the loop when making design changes. This includes material suppliers that are directly connected to the manufacturer. Some collaboration tools for PCB designers include links to suppliers, and providing real-time data on pricing and quantities.
PCB ASSEMBLY TIP 5: CLEAR AND DETAILED DOCUMENTATION
Documenting a PCB design requires designers to clearly define their work regions, meaning they need to mark out their space on the board. Work regions should remain uncluttered and easy to navigate, so designers can focus on their design rather than struggling with software to provide documentation. These tools should also allow designers to easily view the work of other designers on that board, so they can avoid conflicts or duplicated effort.
PCB ASSEMBLY TIP 6: CONTINUOUS IMPROVEMENT AND FEEDBACK
The PCB assembly process can be improved by following the plan-do-check-act (PDCA) cycle. The Plan phase of this approach identifies opportunities for change and plans those changes. The Do phase implements changes on a small scale, while the Check phase analyzes the results to determine the effects of those changes. If the changes are beneficial, the Act phase implements them wider and continuously assesses the results.
Work with the PCB manufacturer to discover new opportunities for improvement, which is an essential component of DFM. This practice also requires collecting and analyzing data to identify areas to reduce scrap, promote assembly cycle times, and improve quality issues while reducing production bottlenecks.
STRENGTHEN PCB ASSEMBLY PROCESS WITH IMAGINEERING: ESSENTIAL STRATEGIES FOR SUCCESS
Many technological advances have improved the reliability and accuracy of PCB assembly, but the challenge is to make the process as seamless and efficient as possible. The best practices discussed above will help improve assembly, especially when combined with an experienced PCB manufacturer like Imagineering. These changes will ultimately accelerate PCB assembly and reduce time-to-market.