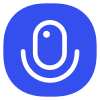
Sign up to save your podcasts
Or
This station is located in the stair core, at the mid-level landing between the first and second floors. At this point you can see the transition of the core structure from CLT to another massive timber material – LVL. While it isn’t typical to see two different massive timber cores stacked on top of each other like this, this has been done here simply to demonstrate that both materials are suitable for use in the core. In contrast to CLT, which is produced on a panel by panel basis, LVL is produced on a rolling press 1.2m wide, meaning that the maximum width of an LVL panel is 1.2m, however the length can be as long as you can transport. Note that LVL is strongest parallel to the grain, and as such depending on the design of the core it may be best aligned vertically – an example of this can be seen at Station 21.
At this horizontal joint between the two massive timber elements you may notice a thin yellow rubber strip. A best practice solution between elements exposed to vibration or impact, these strips are designed to absorb energy, limiting the transfer of vibration between panels. Areas where these strips are required include lift cores, stair cores, or other high impact zones. A great benefit of panelised construction over monolithic structures, the accurate use of these strips can minimise the transfer of structure borne sound, improving internal environmental quality throughout a structure.
Also visible at this station are a number of timber to timber plate connectors. These plates are designed to transfer tensile loads which may be experienced in a core element under wind loads. Note that while these plates have been nail filled, they can also be fixed off using screws.
When you’re ready, keep walking up the stairs to the next station.
This station is located in the stair core, at the mid-level landing between the first and second floors. At this point you can see the transition of the core structure from CLT to another massive timber material – LVL. While it isn’t typical to see two different massive timber cores stacked on top of each other like this, this has been done here simply to demonstrate that both materials are suitable for use in the core. In contrast to CLT, which is produced on a panel by panel basis, LVL is produced on a rolling press 1.2m wide, meaning that the maximum width of an LVL panel is 1.2m, however the length can be as long as you can transport. Note that LVL is strongest parallel to the grain, and as such depending on the design of the core it may be best aligned vertically – an example of this can be seen at Station 21.
At this horizontal joint between the two massive timber elements you may notice a thin yellow rubber strip. A best practice solution between elements exposed to vibration or impact, these strips are designed to absorb energy, limiting the transfer of vibration between panels. Areas where these strips are required include lift cores, stair cores, or other high impact zones. A great benefit of panelised construction over monolithic structures, the accurate use of these strips can minimise the transfer of structure borne sound, improving internal environmental quality throughout a structure.
Also visible at this station are a number of timber to timber plate connectors. These plates are designed to transfer tensile loads which may be experienced in a core element under wind loads. Note that while these plates have been nail filled, they can also be fixed off using screws.
When you’re ready, keep walking up the stairs to the next station.