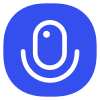
Sign up to save your podcasts
Or
In today's fast-paced business landscape, staying competitive requires continuous process improvement. Companies that do not prioritize optimizing their operations risk falling behind. This is exemplified by Walmart's recent initiative to open five automated distribution centers. By investing in automation, Walmart aims to enhance efficiency, reduce operational costs, and improve customer service, thereby maintaining its competitive edge.
Process improvement involves analyzing and refining workflows to achieve better performance, quality, and efficiency. One of the most recognized methodologies for this is Six Sigma, a data-driven approach that seeks to eliminate defects and variations in processes. Six Sigma uses a set of quality management methods and statistical tools to systematically improve processes and achieve substantial cost savings and quality enhancements.
For any organization, adopting process improvement strategies like Six Sigma can lead to significant benefits:
1. Increased Efficiency: By streamlining processes, companies can reduce waste, minimize errors, and speed up production. This leads to faster delivery times and lower operational costs.
2. Enhanced Quality: Continuous process improvement ensures that products and services meet high-quality standards. This reduces the likelihood of defects and increases customer satisfaction.
3. Cost Reduction: Efficient processes require fewer resources, leading to cost savings. Companies can reinvest these savings into further improvements or new initiatives.
4. Improved Employee Morale: When processes are efficient and less prone to errors, employees experience less frustration and can focus on value-added tasks. This boosts morale and productivity.
5. Adaptability: In a rapidly changing market, the ability to quickly adapt processes is crucial. Continuous improvement fosters a culture of agility and responsiveness to market demands.
Walmart's automation strategy highlights the importance of staying ahead of the curve. By leveraging advanced technologies and process improvement methodologies, companies can maintain their competitive advantage. Implementing Six Sigma and other continuous improvement strategies is not just a one-time effort but an ongoing commitment to excellence.
In conclusion, process improvement is essential for any organization that aims to remain competitive in today's dynamic business environment. Through methodologies like Six Sigma, companies can achieve greater efficiency, quality, and cost savings, positioning themselves for long-term success. As Walmart's example shows, those who invest in continuous improvement are better equipped to meet the challenges of tomorrow.
In today's fast-paced business landscape, staying competitive requires continuous process improvement. Companies that do not prioritize optimizing their operations risk falling behind. This is exemplified by Walmart's recent initiative to open five automated distribution centers. By investing in automation, Walmart aims to enhance efficiency, reduce operational costs, and improve customer service, thereby maintaining its competitive edge.
Process improvement involves analyzing and refining workflows to achieve better performance, quality, and efficiency. One of the most recognized methodologies for this is Six Sigma, a data-driven approach that seeks to eliminate defects and variations in processes. Six Sigma uses a set of quality management methods and statistical tools to systematically improve processes and achieve substantial cost savings and quality enhancements.
For any organization, adopting process improvement strategies like Six Sigma can lead to significant benefits:
1. Increased Efficiency: By streamlining processes, companies can reduce waste, minimize errors, and speed up production. This leads to faster delivery times and lower operational costs.
2. Enhanced Quality: Continuous process improvement ensures that products and services meet high-quality standards. This reduces the likelihood of defects and increases customer satisfaction.
3. Cost Reduction: Efficient processes require fewer resources, leading to cost savings. Companies can reinvest these savings into further improvements or new initiatives.
4. Improved Employee Morale: When processes are efficient and less prone to errors, employees experience less frustration and can focus on value-added tasks. This boosts morale and productivity.
5. Adaptability: In a rapidly changing market, the ability to quickly adapt processes is crucial. Continuous improvement fosters a culture of agility and responsiveness to market demands.
Walmart's automation strategy highlights the importance of staying ahead of the curve. By leveraging advanced technologies and process improvement methodologies, companies can maintain their competitive advantage. Implementing Six Sigma and other continuous improvement strategies is not just a one-time effort but an ongoing commitment to excellence.
In conclusion, process improvement is essential for any organization that aims to remain competitive in today's dynamic business environment. Through methodologies like Six Sigma, companies can achieve greater efficiency, quality, and cost savings, positioning themselves for long-term success. As Walmart's example shows, those who invest in continuous improvement are better equipped to meet the challenges of tomorrow.