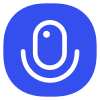
Sign up to save your podcasts
Or
How to Effectively Address Employee Complaints and Prevent OSHA Inspections www.helpwithosha.com Employee complaints are a critical aspect of workplace safety, as they often serve as the primary trigger for OSHA inspections. Addressing these complaints effectively can help organizations maintain a safe work environment while avoiding unnecessary regulatory scrutiny. Here’s a step-by-step guide to managing employee complaints and fostering a culture of safety. Why Employee Complaints Matter An employee complaint, especially one related to safety, is more than just feedback. It reflects how employees feel about their work environment. OSHA’s General Duty Clause mandates employers to protect workers from recognized hazards. If an employee perceives a situation as unsafe—even if it technically complies with regulations—it can escalate into a serious issue if not handled properly. Steps to Handle Employee Complaints Listen and Make Employees Feel Heard When an employee raises a concern, the first priority is to listen actively and empathetically. Employees need to feel that their concerns are taken seriously. Avoid dismissive responses like “This is just part of the job.” Such reactions can erode trust and communication. Investigate the Complaint Conduct a thorough investigation of the issue raised. This includes: Inspecting the area or equipment in question. Taking photos or notes for documentation. Engaging in discussions with relevant team members. Even if the complaint seems minor or unwarranted, investigating shows employees that their concerns matter. Assign Ownership of the Issue Designate someone responsible for resolving the problem. This ensures accountability and follow-through. For example, if warehouse aisles are cluttered with pallets, assign the warehouse manager to find alternative storage solutions. Implement Solutions and Follow Up Depending on the situation, solutions might involve: Adding signage. Providing additional personal protective equipment (PPE). Rearranging workflows or storage layouts. After implementing changes, follow up with the employee who raised the concern to communicate what actions were taken and why. Prevent Future Complaints Regularly review and update safety protocols to address potential hazards proactively. Encourage open communication so employees feel comfortable sharing concerns before they escalate. The Cost of Ignoring Complaints When employees feel ignored, dissatisfaction grows. This can lead to: Passive-aggressive behavior or reduced morale. Escalation of issues through formal complaints to OSHA. Increased risk of citations, fines, or even shutdowns during inspections. For example, in one case, employees complained about cluttered aisles in a warehouse where pallet jack operators were navigating dangerously close to workers. Management initially dismissed the issue due to space constraints but later realized that ignoring it only worsened employee frustration. By assigning ownership and relocating materials, they resolved the problem effectively. Key Takeaways for Employers Employee feelings about safety are as important as actual compliance with regulations. Active listening and prompt action are critical in addressing complaints. Assigning responsibility ensures problems don’t fall through the cracks. Open communication fosters trust and prevents issues from escalating into OSHA inspections. By prioritizing employee concerns and creating a culture of safety, organizations can not only reduce complaints but also improve overall workplace morale and productivity.
5
22 ratings
How to Effectively Address Employee Complaints and Prevent OSHA Inspections www.helpwithosha.com Employee complaints are a critical aspect of workplace safety, as they often serve as the primary trigger for OSHA inspections. Addressing these complaints effectively can help organizations maintain a safe work environment while avoiding unnecessary regulatory scrutiny. Here’s a step-by-step guide to managing employee complaints and fostering a culture of safety. Why Employee Complaints Matter An employee complaint, especially one related to safety, is more than just feedback. It reflects how employees feel about their work environment. OSHA’s General Duty Clause mandates employers to protect workers from recognized hazards. If an employee perceives a situation as unsafe—even if it technically complies with regulations—it can escalate into a serious issue if not handled properly. Steps to Handle Employee Complaints Listen and Make Employees Feel Heard When an employee raises a concern, the first priority is to listen actively and empathetically. Employees need to feel that their concerns are taken seriously. Avoid dismissive responses like “This is just part of the job.” Such reactions can erode trust and communication. Investigate the Complaint Conduct a thorough investigation of the issue raised. This includes: Inspecting the area or equipment in question. Taking photos or notes for documentation. Engaging in discussions with relevant team members. Even if the complaint seems minor or unwarranted, investigating shows employees that their concerns matter. Assign Ownership of the Issue Designate someone responsible for resolving the problem. This ensures accountability and follow-through. For example, if warehouse aisles are cluttered with pallets, assign the warehouse manager to find alternative storage solutions. Implement Solutions and Follow Up Depending on the situation, solutions might involve: Adding signage. Providing additional personal protective equipment (PPE). Rearranging workflows or storage layouts. After implementing changes, follow up with the employee who raised the concern to communicate what actions were taken and why. Prevent Future Complaints Regularly review and update safety protocols to address potential hazards proactively. Encourage open communication so employees feel comfortable sharing concerns before they escalate. The Cost of Ignoring Complaints When employees feel ignored, dissatisfaction grows. This can lead to: Passive-aggressive behavior or reduced morale. Escalation of issues through formal complaints to OSHA. Increased risk of citations, fines, or even shutdowns during inspections. For example, in one case, employees complained about cluttered aisles in a warehouse where pallet jack operators were navigating dangerously close to workers. Management initially dismissed the issue due to space constraints but later realized that ignoring it only worsened employee frustration. By assigning ownership and relocating materials, they resolved the problem effectively. Key Takeaways for Employers Employee feelings about safety are as important as actual compliance with regulations. Active listening and prompt action are critical in addressing complaints. Assigning responsibility ensures problems don’t fall through the cracks. Open communication fosters trust and prevents issues from escalating into OSHA inspections. By prioritizing employee concerns and creating a culture of safety, organizations can not only reduce complaints but also improve overall workplace morale and productivity.