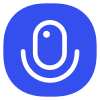
Sign up to save your podcasts
Or
How can the Metal Working Nation close the manufacturing skills gap? As the manufacturing industry continues to grow with the demand for fast and excellent production, it is imperative that the proper skills be found, fostered, and taught. Even with the desirable technological sophistication of the modern manufacturing world, young talent isn’t being found quickly enough to fill the gap left by the retirement of the Baby Boomer generation.
Jim and Jason brainstorm with guest speakers Hernan Ricaurte (Owner of Ricaurte Precision), Brian Grigson (General Manager of Axxis Corporation), and Brain Pendarvis (Owner of Pendarvis Manufacturing) about how manufacturing leaders can take action to influence the next generation of machinists. Be sure to listen to the entire episode to catch the best insights into the real and persisting problem of the manufacturing skills gap!
Connect with us:www.MakingChips.com/contact
Putting a finger on the pulse of the manufacturing skills gapRicaurte, Grigson, and Pendarvis all agree that the skills gap is certainly a major issue of the modern manufacturing world. The “great wave” is here; the older are retiring and the younger aren’t qualified or aren’t interested. Pendarvis shares the struggle of finding talent skilled in the newest manufacturing technology. Leaders know that you can’t just stick anyone on your CNC machines. While the skills gap is a real and present problem, it doesn’t have to remain that way.
Changing the perception of manufacturing is the first step. Most high schoolers don’t even know that trade school for CNC machining or similar work is an option. Many still think that they have to go to college to have a meaningful career. Manufacturing, however, offers so much at such little training cost. Building bridges with your community is the first step to closing the skills gap. Give presentations at the local middle and high schools, invite schools to tour your facilities and show them that what they need - and want - in a career can be found in manufacturing. “It’s not always money that people want,” says Grigson. A clean environment, security, incentives, and evident room for company growth are all attributes that can help your business attract young talent.
Effective training is grounded in effective cultureWho are you as a company? What is your niche? While there is a skills issue, it is important to only hire the skills that you need. What is your company culture? The culture that you want to foster within your business begins with you as the leader. One challenge created by the skills gap is finding someone who is not only talented but also a good fit within your company. Having more experienced employees shadow and oversee the work of new hires or interns provides the opportunity for not only the skills - but for the culture - to be taught.
Ricaurte shares the lessons he learned from studying the manufacturing culture of Japanese machinists. Fostering a culture of accountability and excellence if key. Attention to detail, respect for one another, and the willingness to learn are all necessary to an effective workplace Training the younger generation within that culture will help produce the future talent that you need. Don’t forget to listen to the rest of the episode for more insight into fostering effective culture!
What makes a great modern machinist?It actually depends on the work and skill-set required! With the advancement of technology, the skill sets needed by manufacturers grows more diverse. While not everyone will be adept in all areas of machining, they always need to be willing to learn and grow. Curiosity is a sign of a great future machinist. While genuine curiosity, humility, excellent work ethic, and personal drive are all hard to detect in an interview, they should be attributes that you are striving to discover.
Running an apprenticeship or internship program at your shop is also a highly effective way to discover and nurture new talent. Involve high schoolers in your company’s growth and demonstrate to them the future possibilities within manufacturing. Hiring part-time can also be a good tactic to see if you and your new employee are a good long-term fit.
Finding and providing opportunity in unlikely placesYour local high school isn’t the only place to find potential future talent to invest in. Underprivileged communities are gold when it comes to finding young people with the passion and drive to try something unconventional - such as attending trade school to learn CNC machining. There are bright, curious minds everywhere! Many kids don’t know that manufacturing is even an option among today’s career paths. Manufacturing leaders need to begin investing in and inspiring the talent and ability of young people.
Yes, the manufacturing skills gap is a problem, but it’s not insurmountable. Listen to the full episode to learn more about how you can make a difference in inspiring the next generation of manufacturers!
Here’s The Good Stuff!Subscribe to Making Chips on Apple Podcasts, Google Play, Stitcher, or Spotify
4.7
114114 ratings
How can the Metal Working Nation close the manufacturing skills gap? As the manufacturing industry continues to grow with the demand for fast and excellent production, it is imperative that the proper skills be found, fostered, and taught. Even with the desirable technological sophistication of the modern manufacturing world, young talent isn’t being found quickly enough to fill the gap left by the retirement of the Baby Boomer generation.
Jim and Jason brainstorm with guest speakers Hernan Ricaurte (Owner of Ricaurte Precision), Brian Grigson (General Manager of Axxis Corporation), and Brain Pendarvis (Owner of Pendarvis Manufacturing) about how manufacturing leaders can take action to influence the next generation of machinists. Be sure to listen to the entire episode to catch the best insights into the real and persisting problem of the manufacturing skills gap!
Connect with us:www.MakingChips.com/contact
Putting a finger on the pulse of the manufacturing skills gapRicaurte, Grigson, and Pendarvis all agree that the skills gap is certainly a major issue of the modern manufacturing world. The “great wave” is here; the older are retiring and the younger aren’t qualified or aren’t interested. Pendarvis shares the struggle of finding talent skilled in the newest manufacturing technology. Leaders know that you can’t just stick anyone on your CNC machines. While the skills gap is a real and present problem, it doesn’t have to remain that way.
Changing the perception of manufacturing is the first step. Most high schoolers don’t even know that trade school for CNC machining or similar work is an option. Many still think that they have to go to college to have a meaningful career. Manufacturing, however, offers so much at such little training cost. Building bridges with your community is the first step to closing the skills gap. Give presentations at the local middle and high schools, invite schools to tour your facilities and show them that what they need - and want - in a career can be found in manufacturing. “It’s not always money that people want,” says Grigson. A clean environment, security, incentives, and evident room for company growth are all attributes that can help your business attract young talent.
Effective training is grounded in effective cultureWho are you as a company? What is your niche? While there is a skills issue, it is important to only hire the skills that you need. What is your company culture? The culture that you want to foster within your business begins with you as the leader. One challenge created by the skills gap is finding someone who is not only talented but also a good fit within your company. Having more experienced employees shadow and oversee the work of new hires or interns provides the opportunity for not only the skills - but for the culture - to be taught.
Ricaurte shares the lessons he learned from studying the manufacturing culture of Japanese machinists. Fostering a culture of accountability and excellence if key. Attention to detail, respect for one another, and the willingness to learn are all necessary to an effective workplace Training the younger generation within that culture will help produce the future talent that you need. Don’t forget to listen to the rest of the episode for more insight into fostering effective culture!
What makes a great modern machinist?It actually depends on the work and skill-set required! With the advancement of technology, the skill sets needed by manufacturers grows more diverse. While not everyone will be adept in all areas of machining, they always need to be willing to learn and grow. Curiosity is a sign of a great future machinist. While genuine curiosity, humility, excellent work ethic, and personal drive are all hard to detect in an interview, they should be attributes that you are striving to discover.
Running an apprenticeship or internship program at your shop is also a highly effective way to discover and nurture new talent. Involve high schoolers in your company’s growth and demonstrate to them the future possibilities within manufacturing. Hiring part-time can also be a good tactic to see if you and your new employee are a good long-term fit.
Finding and providing opportunity in unlikely placesYour local high school isn’t the only place to find potential future talent to invest in. Underprivileged communities are gold when it comes to finding young people with the passion and drive to try something unconventional - such as attending trade school to learn CNC machining. There are bright, curious minds everywhere! Many kids don’t know that manufacturing is even an option among today’s career paths. Manufacturing leaders need to begin investing in and inspiring the talent and ability of young people.
Yes, the manufacturing skills gap is a problem, but it’s not insurmountable. Listen to the full episode to learn more about how you can make a difference in inspiring the next generation of manufacturers!
Here’s The Good Stuff!Subscribe to Making Chips on Apple Podcasts, Google Play, Stitcher, or Spotify
218 Listeners
36 Listeners
102 Listeners
100 Listeners
30 Listeners
6 Listeners
15 Listeners
13 Listeners
22 Listeners
0 Listeners
34 Listeners
3 Listeners
26 Listeners
11 Listeners
3 Listeners