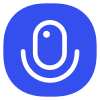
Sign up to save your podcasts
Or
I wanted to differentiate myself among other machine shops in the area with the new Carr Machine & Tool location. The shop floor is where we make our money. I took extra steps in the process to create a new image for my shop. I wanted to present it in a way that was sophisticated, high-tech, polished, and professional—while remaining efficient.
That’s where IMEC came in. I reached out to them for some technical collaboration to help design an efficient shop floor. I worked with both Dean Harms and Tim Maurer and it was an amazing experience. So in this episode of Making Chips, I’m sharing what the collaboration and design process looked like with IMEC.
SegmentsDean Harms is a Regional Manager with IMEC. It’s his mission to help others any way he can on a daily basis and have fun along the way. Sounds like us, right?
IMEC is part of the Manufacturing Extension Partnership (MEP) National Network. It’s connected to the US Department of Commerce through the NIST organization. IMEC launched in the 1990s and is about to celebrate its 25th anniversary. There are 51 MEPs (one in every state + Puerto Rico). Their overall mission is to provide solutions and improvements to small and medium-sized manufacturing companies to help them navigate the changing landscape, drive profitability, sustain growth, and become globally competitive.
IMEC is a non-profit that is both privately and publicly funded. They are a channel that brings tax dollars back into the state of Illinois by specifically serving manufacturing businesses. Dean Harms makes sure the money is applied where it’s needed most.
My experience working with IMECDean cold-called me after I was on a live Facebook interview. I mentioned I was about to move my shop, so he reached out. He knew that there was probably something IMEC could do to help with the move. I heard that they could help design my shop floor and I really wanted a high-end polished shop. Dean introduced me to Tim Maurer and said he would be the perfect guy to collaborate with to design my shop floor. Tim has decades of experience not only with IMEC but also with Caterpillar. After I met Tim, I knew I was dealing with someone who was competent and knew what a manufacturing floor should look like.
The shop floor design processTim’s design process was thorough, starting with the vision for our future and ending with the execution of the move. We started by setting objectives: Where did we want to be? What type of work would we be doing? What new technologies will be utilized on the shop floor?
We did a physical walk of both of the properties. He took physical measurements of the new building, all of our tools, and made sure the room was big enough for a CMM. After he did the physical layout, we met again to go over the flow of the room and nail down the workflow. We placed the machinery and equipment in the prime areas of the floor to maximize the square footage.
He established power needs, air drops, water needs, an eyewash station, etc. He developed the CAD and we talked about future automation and made sure they’d be room around the machines. He delivered the final layout to us in a CAD model. The best part? On moving day we had a roadmap to mark where everything went. We knew where every single thing would go.
The design process was an investment in our future productivity. I would never have completed this process as well as Tim did. I highly recommend working with IMEC through a big move to create a more efficient shop floor. Don’t be afraid to delegate design to the experts.
BAM!
– Jim
Resources mentioned on this episodeGet The Boring Bar Newsletter - Text CHIPS to 38470 to subscribe!
4.7
114114 ratings
I wanted to differentiate myself among other machine shops in the area with the new Carr Machine & Tool location. The shop floor is where we make our money. I took extra steps in the process to create a new image for my shop. I wanted to present it in a way that was sophisticated, high-tech, polished, and professional—while remaining efficient.
That’s where IMEC came in. I reached out to them for some technical collaboration to help design an efficient shop floor. I worked with both Dean Harms and Tim Maurer and it was an amazing experience. So in this episode of Making Chips, I’m sharing what the collaboration and design process looked like with IMEC.
SegmentsDean Harms is a Regional Manager with IMEC. It’s his mission to help others any way he can on a daily basis and have fun along the way. Sounds like us, right?
IMEC is part of the Manufacturing Extension Partnership (MEP) National Network. It’s connected to the US Department of Commerce through the NIST organization. IMEC launched in the 1990s and is about to celebrate its 25th anniversary. There are 51 MEPs (one in every state + Puerto Rico). Their overall mission is to provide solutions and improvements to small and medium-sized manufacturing companies to help them navigate the changing landscape, drive profitability, sustain growth, and become globally competitive.
IMEC is a non-profit that is both privately and publicly funded. They are a channel that brings tax dollars back into the state of Illinois by specifically serving manufacturing businesses. Dean Harms makes sure the money is applied where it’s needed most.
My experience working with IMECDean cold-called me after I was on a live Facebook interview. I mentioned I was about to move my shop, so he reached out. He knew that there was probably something IMEC could do to help with the move. I heard that they could help design my shop floor and I really wanted a high-end polished shop. Dean introduced me to Tim Maurer and said he would be the perfect guy to collaborate with to design my shop floor. Tim has decades of experience not only with IMEC but also with Caterpillar. After I met Tim, I knew I was dealing with someone who was competent and knew what a manufacturing floor should look like.
The shop floor design processTim’s design process was thorough, starting with the vision for our future and ending with the execution of the move. We started by setting objectives: Where did we want to be? What type of work would we be doing? What new technologies will be utilized on the shop floor?
We did a physical walk of both of the properties. He took physical measurements of the new building, all of our tools, and made sure the room was big enough for a CMM. After he did the physical layout, we met again to go over the flow of the room and nail down the workflow. We placed the machinery and equipment in the prime areas of the floor to maximize the square footage.
He established power needs, air drops, water needs, an eyewash station, etc. He developed the CAD and we talked about future automation and made sure they’d be room around the machines. He delivered the final layout to us in a CAD model. The best part? On moving day we had a roadmap to mark where everything went. We knew where every single thing would go.
The design process was an investment in our future productivity. I would never have completed this process as well as Tim did. I highly recommend working with IMEC through a big move to create a more efficient shop floor. Don’t be afraid to delegate design to the experts.
BAM!
– Jim
Resources mentioned on this episodeGet The Boring Bar Newsletter - Text CHIPS to 38470 to subscribe!
218 Listeners
36 Listeners
102 Listeners
100 Listeners
30 Listeners
6 Listeners
15 Listeners
13 Listeners
22 Listeners
0 Listeners
34 Listeners
3 Listeners
26 Listeners
11 Listeners
2 Listeners