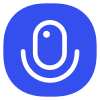
Sign up to save your podcasts
Or
We have an Instagram! Go give us a follow @incrementalci and see all types of improvements from across the web!
On this episode Devin Bodony and Uriel Eisen talk about Production Leveling and the three M's of the Toyota Production System. Muda, Mura, and Muri. There are many examples where increasing inventory can help level production which can be hugely valuable. Uneven production leads to huge waste so it is critical to figure out how to level production. While Toyota uses temp workers to deal with peaks in demand, that is not necessarily a tool that is available to small business. Devin and Uriel discuss many ways that a business can achieve flex to deal with peaks and valleys in demand but the root of the issues is an uneven load on the shop. This uneven load necessitates optimizing systems for peak demand which is wasteful. There is a lot of efficiency to be gained by keeping a leaner system continuously busy. They discuss staggered work schedules, working overtime, using pricing adjustments to deal with fluctuations.
Some discussion of improvements, keeping things simple and production rationalizations. It points to the need for good SOPs and developing a culture that works from SOPs rather that everyone doing things differently. Checklist Manifesto is a great book that is very relavant here and worth a read. Devin talks through the strugles of information handoff from CAM to the CNC operator. What is the process and tools for making sure that information is handed off well and absent rework. A discussion of checklists vs detailed instructions. Toyota uses a combination of these things and it is interesting to see where they use which one.
Uriel discusses kanban signals and how many kanban to have in a given item's stock. It is clear that efficiency would be increased paradoxically by reducing the efficiency of the paint department.
TPS has a simultaneous focus on the global view and on the minute. The very big and the very small. How do we maintain focus on those two opposites as people that run the business as well as work in the business.
Is counting down less mentally taxing than counting to a target that you need to hold in mind? That said, counting in general is all waste. We should all move away from needing to count.
5
55 ratings
We have an Instagram! Go give us a follow @incrementalci and see all types of improvements from across the web!
On this episode Devin Bodony and Uriel Eisen talk about Production Leveling and the three M's of the Toyota Production System. Muda, Mura, and Muri. There are many examples where increasing inventory can help level production which can be hugely valuable. Uneven production leads to huge waste so it is critical to figure out how to level production. While Toyota uses temp workers to deal with peaks in demand, that is not necessarily a tool that is available to small business. Devin and Uriel discuss many ways that a business can achieve flex to deal with peaks and valleys in demand but the root of the issues is an uneven load on the shop. This uneven load necessitates optimizing systems for peak demand which is wasteful. There is a lot of efficiency to be gained by keeping a leaner system continuously busy. They discuss staggered work schedules, working overtime, using pricing adjustments to deal with fluctuations.
Some discussion of improvements, keeping things simple and production rationalizations. It points to the need for good SOPs and developing a culture that works from SOPs rather that everyone doing things differently. Checklist Manifesto is a great book that is very relavant here and worth a read. Devin talks through the strugles of information handoff from CAM to the CNC operator. What is the process and tools for making sure that information is handed off well and absent rework. A discussion of checklists vs detailed instructions. Toyota uses a combination of these things and it is interesting to see where they use which one.
Uriel discusses kanban signals and how many kanban to have in a given item's stock. It is clear that efficiency would be increased paradoxically by reducing the efficiency of the paint department.
TPS has a simultaneous focus on the global view and on the minute. The very big and the very small. How do we maintain focus on those two opposites as people that run the business as well as work in the business.
Is counting down less mentally taxing than counting to a target that you need to hold in mind? That said, counting in general is all waste. We should all move away from needing to count.
16,080 Listeners
1,877 Listeners
218 Listeners
56,176 Listeners
36 Listeners
33 Listeners
102 Listeners
9 Listeners
30 Listeners
6 Listeners
2 Listeners
22 Listeners
34 Listeners
5 Listeners
2 Listeners