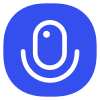
Sign up to save your podcasts
Or
This week Devin and Uriel talk through some listener questions, talk production leveling, how to prioritize tasks, and what happens when linked processes fail.
Standardized tooling and redundant tooling can be an essential part of gaining efficiency. It is interesting to think about what can be standardized but also how to standardize deviation from standard... Is that possible? Kanban can be a very useful tool for making sure that tools stay in stock. As buffers get reduced, downtime becomes more immediately problematic so it needs to be addressed.
What's the best way to get started in lean and what are some favorite cheap and quick improvements.
Developing in house vs buying off the shelf or hiring out custom machines. Toyota talks about building in house costing 1/3-1/5 the cost of buying. What are they talking about?
Figuring out what to do next minute by minute in the shop is very tricky. It is hard to build systems that surface what should be done in what order but if we just write out a schedule ahead of time, than it will be rigid and will not respond to fluctuations in the market.
What happens when things fail in a system of linked processes with minimal buffers, it becomes immediately apparent that there was a problem. Adding inventory buffers between processes can alleviates this issue, but bakes in a lot of waste.
Devin and Uriel discuss some improvements that they made during the week with some interesting conversations around what issues were noticed that led to the improvements.
5
55 ratings
This week Devin and Uriel talk through some listener questions, talk production leveling, how to prioritize tasks, and what happens when linked processes fail.
Standardized tooling and redundant tooling can be an essential part of gaining efficiency. It is interesting to think about what can be standardized but also how to standardize deviation from standard... Is that possible? Kanban can be a very useful tool for making sure that tools stay in stock. As buffers get reduced, downtime becomes more immediately problematic so it needs to be addressed.
What's the best way to get started in lean and what are some favorite cheap and quick improvements.
Developing in house vs buying off the shelf or hiring out custom machines. Toyota talks about building in house costing 1/3-1/5 the cost of buying. What are they talking about?
Figuring out what to do next minute by minute in the shop is very tricky. It is hard to build systems that surface what should be done in what order but if we just write out a schedule ahead of time, than it will be rigid and will not respond to fluctuations in the market.
What happens when things fail in a system of linked processes with minimal buffers, it becomes immediately apparent that there was a problem. Adding inventory buffers between processes can alleviates this issue, but bakes in a lot of waste.
Devin and Uriel discuss some improvements that they made during the week with some interesting conversations around what issues were noticed that led to the improvements.
16,080 Listeners
1,877 Listeners
218 Listeners
56,170 Listeners
36 Listeners
33 Listeners
102 Listeners
9 Listeners
30 Listeners
6 Listeners
2 Listeners
22 Listeners
34 Listeners
5 Listeners
2 Listeners