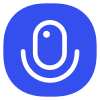
Sign up to save your podcasts
Or
Episode page with transcript and more
My guest for Episode #484 of the Lean Blog Interviews Podcast is Keith Ingels, who previously joined us in Episode 390. He's the RLM Manager of Solutions & Support Centers — RLM being the Raymond Lean Management system.
He was also a guest with me for Episode 62 of “My Favorite Mistake.” His story and insights were also featured in Chapter 8 of my book, The Mistakes That Make Us: Cultivating a Culture of Learning and Innovation.
In today's episode, we discuss how the Raymond Corporation makes Lean / TPS their own management system, even while being under the Toyota corporate umbrella. RLM focuses on developing people and that starts with leaders. Why does a culture of continuous improvement start with small steps and not requiring ROI calculations for every improvement? We discuss how kaizen participation rates are a leading indicator of employee morale and how absenteeism and turnover are lagging indicators. We talk about that and more…
“Critique the process, not the people.”
The podcast is sponsored by Stiles Associates, now in its 30th year of business. They are the go-to Lean recruiting firm serving the manufacturing, private equity, and healthcare industries. Learn more.
This podcast was also brought to you by Arena, a PTC Business. Arena is the proven market leader in Cloud Product Lifecycle Management (PLM) with over 1,400 customers worldwide. Visit the link arenasolutions.com/lean to learn more about how Arena can help speed product releases with one connected system.
This podcast is part of the #LeanCommunicators network.
4.6
4545 ratings
Episode page with transcript and more
My guest for Episode #484 of the Lean Blog Interviews Podcast is Keith Ingels, who previously joined us in Episode 390. He's the RLM Manager of Solutions & Support Centers — RLM being the Raymond Lean Management system.
He was also a guest with me for Episode 62 of “My Favorite Mistake.” His story and insights were also featured in Chapter 8 of my book, The Mistakes That Make Us: Cultivating a Culture of Learning and Innovation.
In today's episode, we discuss how the Raymond Corporation makes Lean / TPS their own management system, even while being under the Toyota corporate umbrella. RLM focuses on developing people and that starts with leaders. Why does a culture of continuous improvement start with small steps and not requiring ROI calculations for every improvement? We discuss how kaizen participation rates are a leading indicator of employee morale and how absenteeism and turnover are lagging indicators. We talk about that and more…
“Critique the process, not the people.”
The podcast is sponsored by Stiles Associates, now in its 30th year of business. They are the go-to Lean recruiting firm serving the manufacturing, private equity, and healthcare industries. Learn more.
This podcast was also brought to you by Arena, a PTC Business. Arena is the proven market leader in Cloud Product Lifecycle Management (PLM) with over 1,400 customers worldwide. Visit the link arenasolutions.com/lean to learn more about how Arena can help speed product releases with one connected system.
This podcast is part of the #LeanCommunicators network.
177 Listeners
30,845 Listeners
200 Listeners
15 Listeners
27 Listeners
111,917 Listeners
9,190 Listeners
21 Listeners
184 Listeners
9 Listeners
9,236 Listeners
2,190 Listeners
21 Listeners
38 Listeners
613 Listeners
15,335 Listeners
15 Listeners
152 Listeners